レーザー溶接の基本特性
レーザー溶接ロボットは、ロボットアームの先端にレーザー加工ヘッドを設置し、レーザーを照射させて溶接するアプリケーションです。
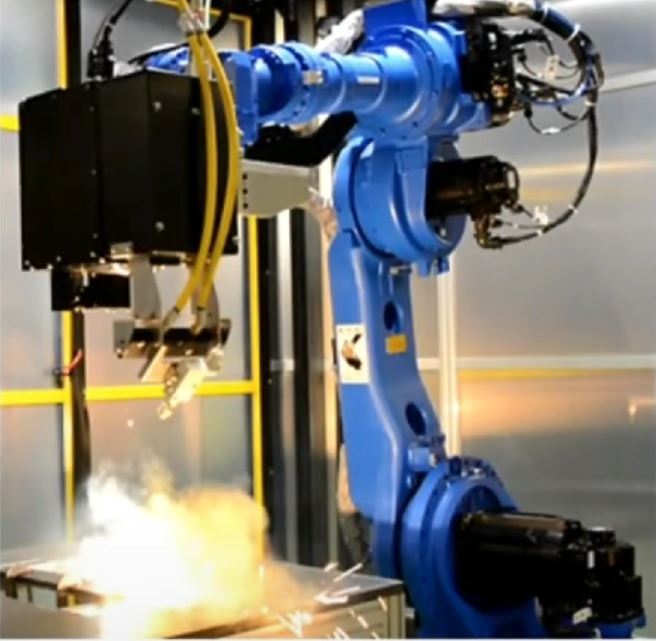
近年では、お客さまからの溶接速度や溶接品質への要求が高まり、レーザー溶接への関心が高まっています。レーザー溶接は溶接点の集光スポット径がおよそ1mmと極小で、エネルギー密度が高いため、熱影響部が小さく且つ溶け込みが深い溶接ができます。例えば板厚10mm程度の対象をアーク溶接で溶接する場合は、V字に開先を切ってV字の部分を溶接ビードで盛る必要がありますが、レーザー溶接では開先を作らず突き合せた箇所を溶接することができます。開先部分がないので熱歪みが発生しにくく、高速で高品質な溶接となります。
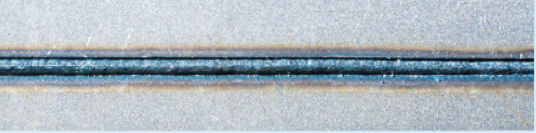
しかし、集光スポット径が小さいので隙間があると未接合部分が発生するなどの溶接対象の前加工の精度も要求されます。
一方で、集光スポット径より幅広の溶接線が要求されるような場合は、レーザー加工ヘッド内で照射方向を「8の字」や「のの字」のようなパターンに高速で移動させて太い溶接線を確保する溶接、いわゆるウォブリング溶接にすることができます。
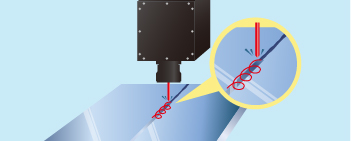
照射方向を移動させるガルバノスキャナーヘッド
ロボットアームの先端に装着するレーザー加工ヘッド内で照射方向を移動することが可能なものはガルバノスキャナーヘッドと呼ばれ、その特長としては、照射ヘッドレーザー光を任意の方向へ反射させるミラーとミラーの角度を高性能モータで精密制御して光を移動させています。ガルバノスキャナ―ヘッドはミラー機構を持たない通常のレーザー加工ヘッドに比べ大きさと重さがあることから多くは可搬質量が25~50キロ程度の中型ロボットが採用されています。レーザー溶接の特長として溶接対象の厚み・形状・材質に合わせた最適な溶接条件の検討を効率的に行えるほか、溶接途中での条件変更も可能なことも挙げられます。

レーザー溶接が使用されている産業と導入のメリット/デメリット
レーザー溶接が使われている産業には主に自動車のシート骨格やボディー、コピー機などの内部フレーム、板金の製造業が挙げられます。
レーザー溶接の導入にさいしては、アーク溶接の1.5倍~4倍の高出力レーザー照射ができるメリットがある一方、レーザー発振器のほか、レーザー照射ヘッド、ロボットアームとの組合せや制御方法などの検討項目と手間が必要になります。またレーザー発振器が高額なので、アーク溶接やスポット溶接に比べて導入コストが高くなるデメリットもあります。
安川電機での取り組みとデータ活用
当社で開発している小型軽量レーザー照射ヘッドは、可搬質量が25キロの中型多用途適用型ロボットに搭載が可能で、設備設置面積(フットプリント)の省スペース化につながっています。アイキューブメカトロニクスの自動化+デジタル活用を進めるなかでは、レーザー長(深度)、照射温度、スポット径、照射時間、反射角度、といったデータを視える化し、どういう条件で照射して、その結果どのような溶接品質になったのかを分析することで生産の改善につなげていくことができます。
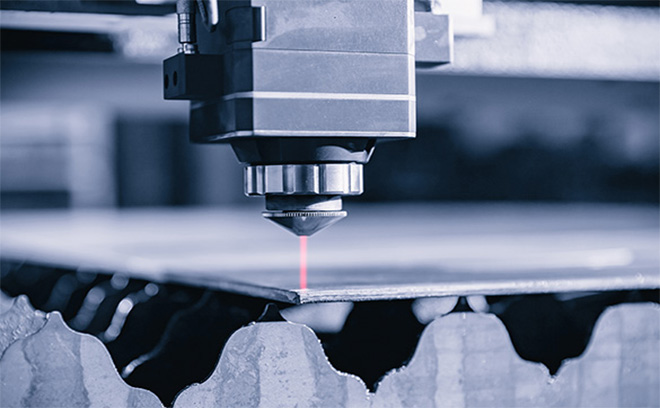
関連する製品