アーク溶接の基本特性
アーク溶接は、産業用ロボットのアームの先端に溶接トーチを装着し、アーク放電を起こして金属同士を接合する溶接方法の一つで、分かりやすくいうと”点”ではなく”線状”に溶接を行なっていくアプリケーションです。アーク放電は、溶接トーチの先端から電極となる溶接ワイヤに電流を流し、接合したい金属に接触させてスパークさせてから起こります。
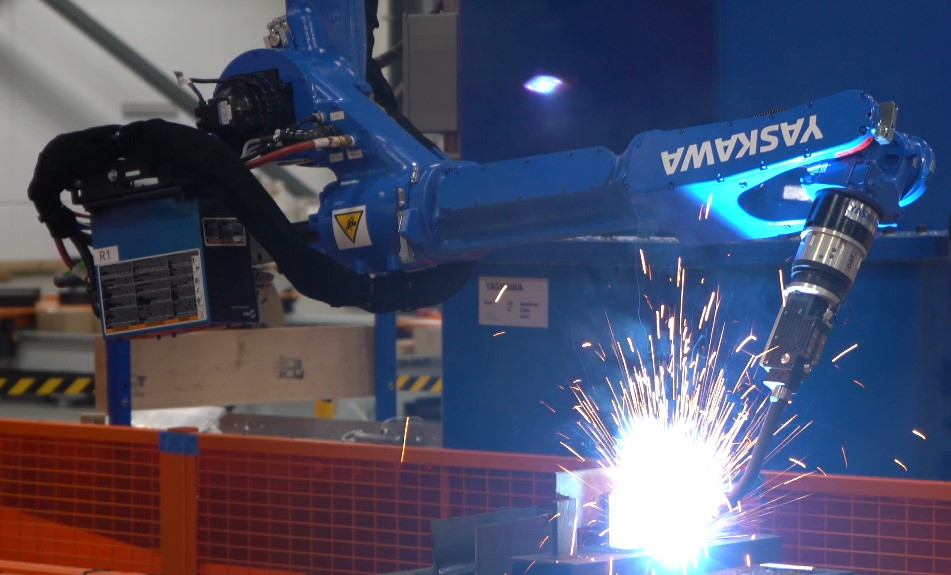
アークは最高2万℃にも達するほど高温なため、ほとんどの金属が素早く溶け、接合できる状態になります。アーク溶接における溶接品質を決めるのは、どれだけキメの細かい均一な”ビード”と呼ばれる形状に盛り作れるかになりますが、このなめらかなビード形状にするために、ロボットアームの先端に装着したトーチの軌跡を精密にモーション制御することで高速かつ高品質な溶接となります。
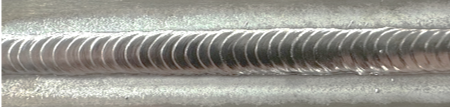
アーク溶接を行うと、火花のようなスパッタが飛び散ります。これは実は溶けたワイヤが溶接対象の金属に溶け込まず微細な粒になって飛び散っているので、飛び散ったスパッタが溶接対象の表面に当たると冷えて付着してしまい溶接対象の品質が落ちてしまうため、できるだけスパッタが少ない溶接が求められています。溶接ビードの品質差により接合部分の劣化に違いがでるので、当社では自社の溶接電源に対して、溶接時の電流を制御したり溶接ワイヤの送給を制御したりする技術を開発して溶接品質の向上に取り組んでいます。
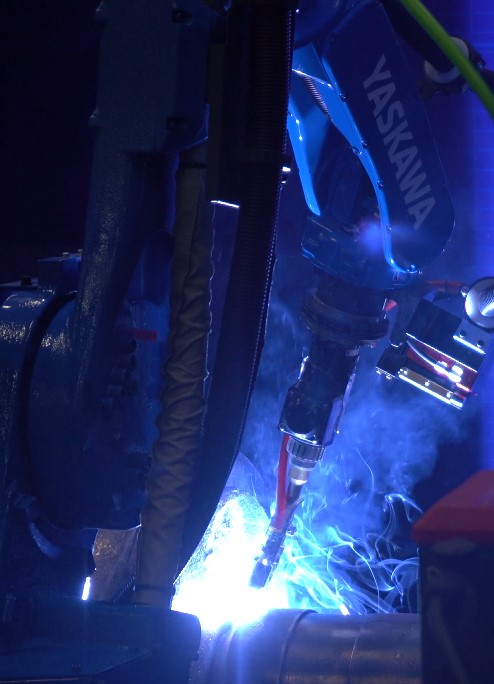
アーク溶接が使用されている産業と導入のメリット/デメリット
アーク溶接が最も多く使われているのは自動車産業です。特にマフラーや車体の骨格部分、サスペンションの部品、シートの骨格などの溶接など、自動車の足回り部品といった高い溶接品質が求められる部分に使われています。また昨今のグローバルでのEV化の流れのなかでも二次電池(バッテリー)ケースのアルミ溶接などで使用されています。そして最近では一般産業でも大型機械や建設機械、ボイラーなどの溶接工程などで幅広く使われています。アーク溶接ロボットの特長としては、溶接スピードが速く作業ができることに加えて、製品の品質が安定することなどが挙げられます。
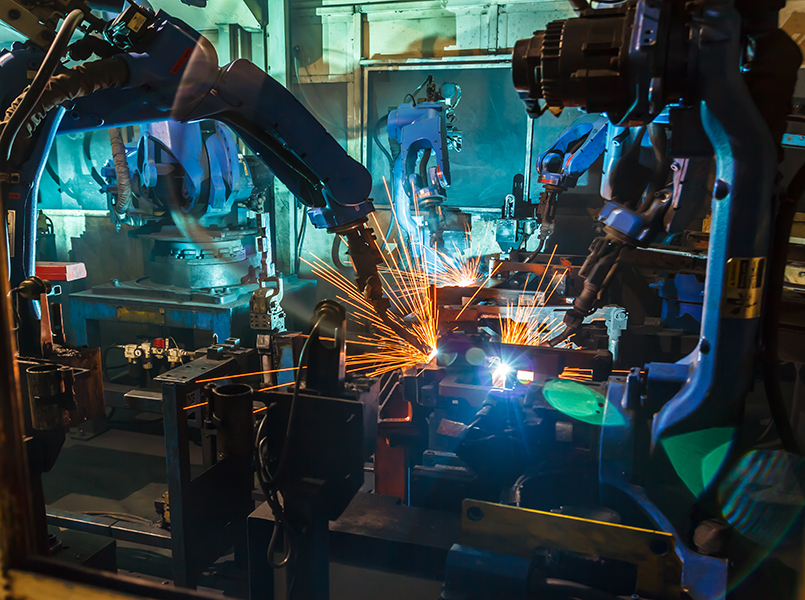
また、大型のガンの装着が必要になるスポット溶接ロボットと比べると可搬質量が15キロ程度の小型なロボットが用いられ広い面積を接合できるといったメリットもありますが、一方で溶接部分を水平に近い状態に適切に保つ必要があるため、ワークを保持するポジショナーなどで周辺設備が大きくなるデメリットもあります。
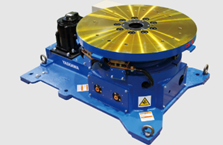
安川電機での取り組みとデータ活用
アーク溶接におけるデジタルデータの活用という点では、溶接電流や溶接電圧のような加工データを取得しながら、溶接品質に問題が発生していないかを確認することで、生産性改善などが期待できます。また最新の取り組みとして可搬質量が10キロの人協働ロボットにアーク溶接のトーチを装着することで、ロボットが作業している横で作業員が溶接ヘルメットをかぶり、溶接状況を確認しながら作業を行うことができる試みも行っています。これにより、現場で使われている半自動溶接機と接続することで人が溶接している作業をそのままロボットに置き換えることができます。
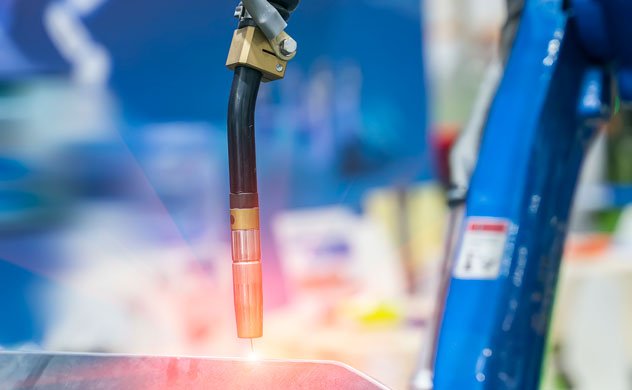
関連する製品