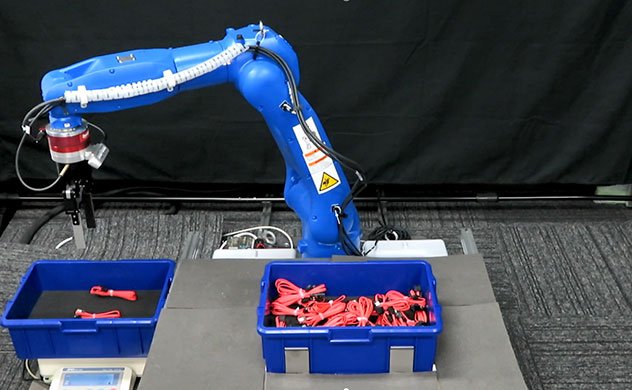
これまで産業用ロボットにビジョンシステムを付加してバラ積みピッキングをさせる場合は、工業部品など剛体物であれば対象物をつかむ場所のパターンが一定化されているため実用化はできていました。ただ、ケーブルなど軟体物や不定形物のピッキングとなると個体差があるため自動化が難しく人手に頼るしかありませんでした。
そこで独自開発したAI技術「Alliom(アリオム)」を活用することで、シミュレータ上でより現実環境に近い学習データを作成し剛体物だけでなく軟体物も同一ハンドでピッキングができるようになります。シミュレータ上でAI生成プロセス(学習データ生成+学習+AI生成)が完結できるため、AI開発含めて実運用までの導入時間が圧倒的に短くなり、実機投入精度の向上も図れます。
例えばバラ積み部品のピッキング作業であれば、対象の部品をシミュレータに取り込み、AIで仮想空間上に部品の摩擦感や光源の角度などを含め、現実に限りなく近づけた作業環境を構築します。AIでバーチャル上に大量の部品データとバラバラの積み方を生成することで、ロボットハンドがどの軌道でどのポイントであれば安定して把持できるのか学習していき、これが繰り返されることで精度が上がっていきます。

これまで実機で生成していた学習用のデータが不要になり、3-4時間ほどで実機検証して適用できるようになり、導入にかかる時間やコストの大幅な削減につながります。最終的に対象は同じハンドで金属品などの硬い部品から唐揚げなど不定形物まで、取り出すことができます。
ほかにも鋳物の外観検査などそもそも不良品が出にくくビッグデータ化に時間がかかる工程でも、数十枚の画像からシミュレーションでリアルな不良データをつくり、実装可能なAIを生成します。ロボットとカメラを連携してキズを検査する工程など同技術の適用範囲を広げていきます。
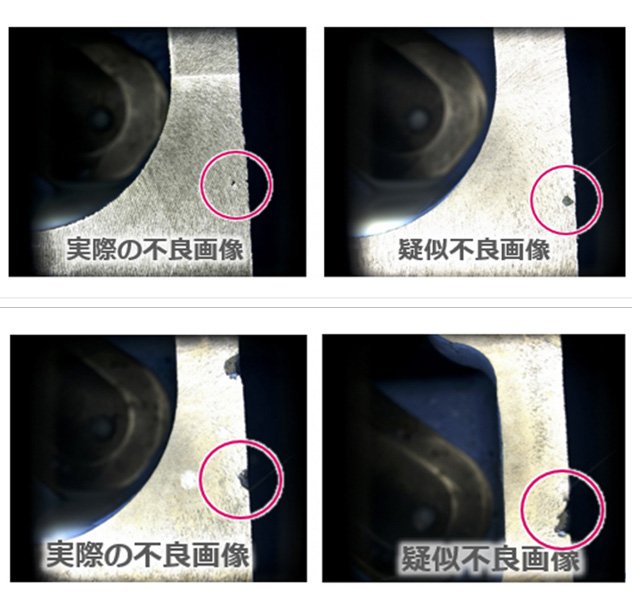