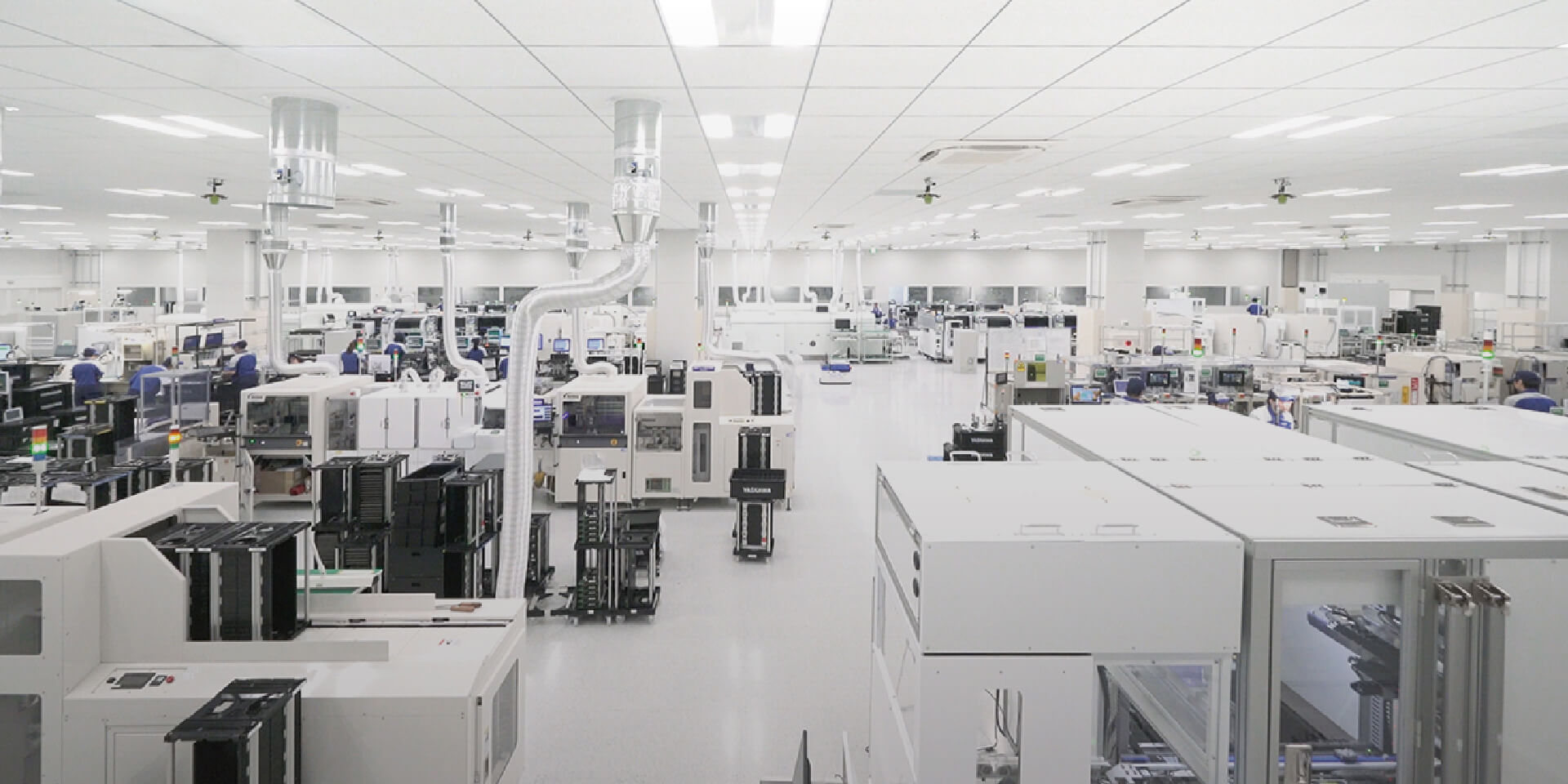
Project Story | 01
メカトロニクス製品に
データ活用を融合し、
飛躍的な生産性向上を実現する、
最新の次世代工場。
2017年7月、「ものづくりとビジネスを変える次世代工場」をコンセプトとする「安川ソリューションファクトリ」が稼働。工場の生産スピードと効率は従来の3倍、リードタイムは6分の1に短縮するなど飛躍的な生産性向上を達成した。それらを実現するまでに、プロジェクトチームはどのような苦労を乗り越え、どのように技術の壁を突破したのか。工場全体の工程設計と生産ライン構築・評価を担った、矢括 俊幸に語ってもらった。
MEMBER
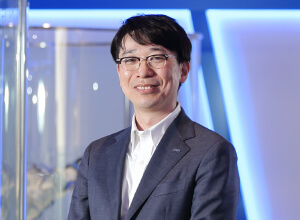
- 生産
- 矢括 俊幸
- 2008年入社
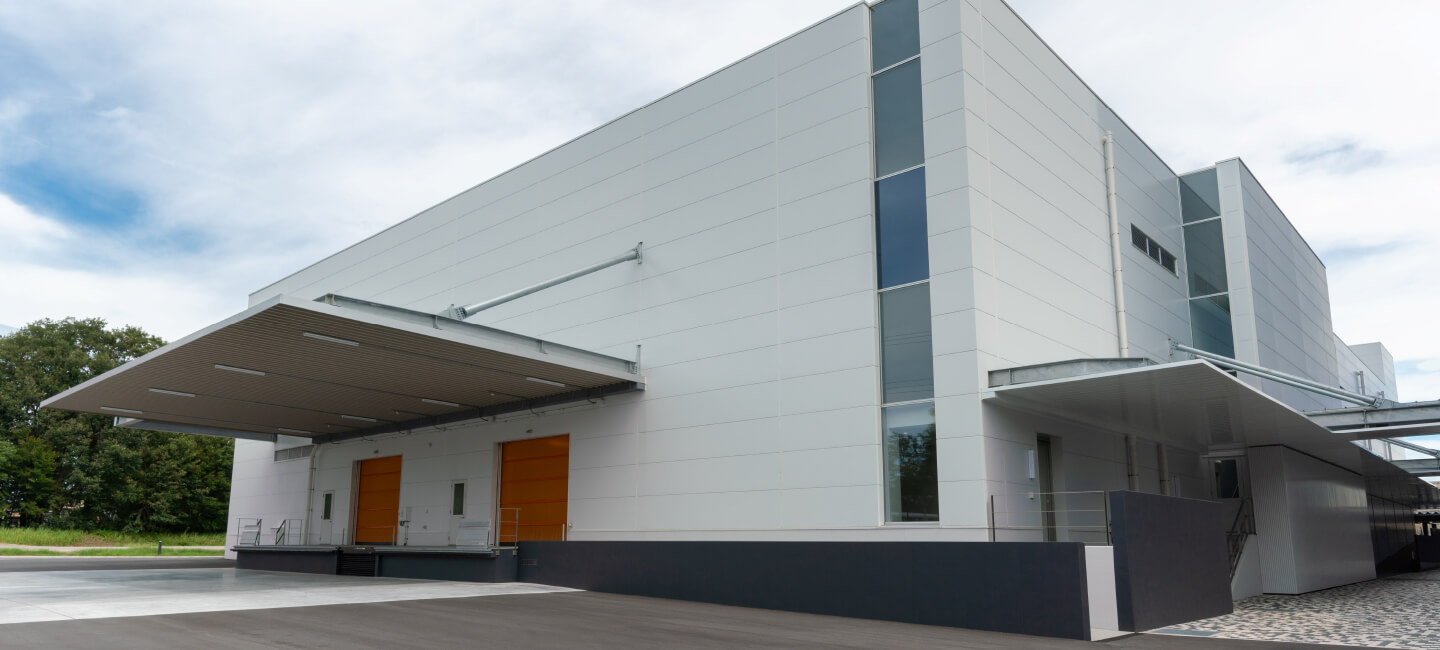
これまで安川電機が培ってきた、
自動化技術を最大限に活かして
2017年4月、安川ソリューションファクトリ(以下、Y’sF)構築のプロジェクトに参画した時、それまで製造実行管理システム(Manufacturing Execution System:MES)の企画立案・システム構築、グローバル展開に携わっていた矢括は胸を高鳴らせていた。「これまで取り組んできたMESにつながる次のステップのプロジェクトがいよいよ始まるのだ」と。
「MESは工場全体というより、あるラインで実証していました。一方、当プロジェクトは工場全体で設備・機器とシステムを連携して、いわば次世代工場を作るというもの。こうした試みは当社としても私自身も初めての経験であり、苦労は予想されるものの、それ以上に期待感が高まりました」
安川電機が、「メカトロニクス製品にデータ活用を融合し、持続的な生産性向上を実現するソリューションを提供する」という「i³-Mechatronics(アイキューブ メカトロニクス)」を打ち出したのは2017年。Y’sFのミッションの一つは、安川電機が半世紀以上にわたって培ってきた自動化技術(自社のロボット、サーボ、インバータ、コントローラ、IoT、AI)を活用して、「i3-Mechatronics」の実証を行うことだ。また同時に、安川電機では、「市場要求納期を必ず守る」「人手のかからないものづくり」「データで改善する仕組み」を実現する生産システムの実現を目指す「Y’s production25」を始動。Y’sFは、「Y’s production25」のモデル工場としての役割も担っているのだ。
これらのミッションを負うプロジェクトチームが最初に決めたのは、「生産性3倍、リードタイム6分の1を達成する」という明確な数字目標だった。「正直、かなり無理があるなと思いました(苦笑)。生産性3倍とは、単純に言えば、現在3人でしている仕事を1人でできるようにするということ。さらなる自動化はもちろん、作業の効率化をいかに実現するか、一つ一つ潰していく必要があり、それは途方もなく骨の折れる仕事に思えました」
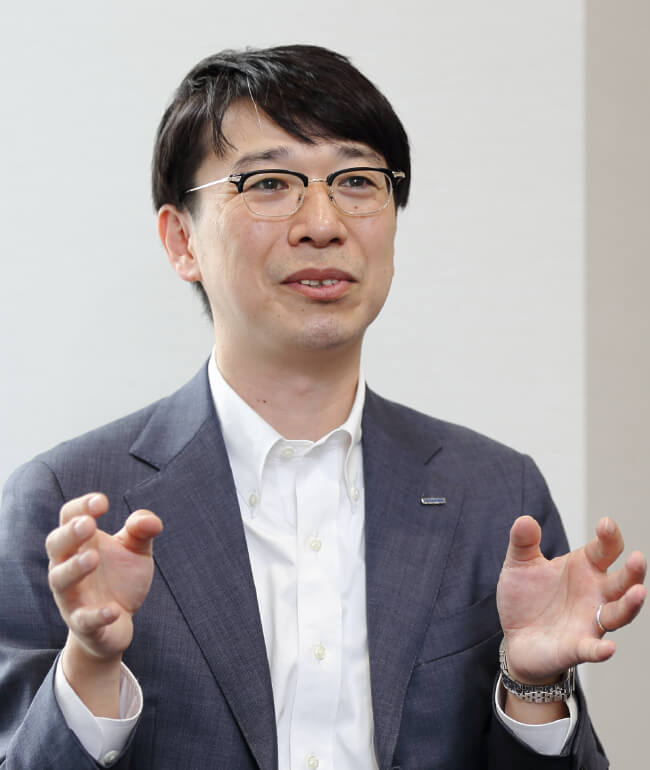
データ活用を軸とした
自動化領域の拡大へ
「生産性3倍、リードタイム6分の1」を達成するための取り組みの一つは、 データ活用を軸とした自動化領域の拡大だ。「生産性や品質を維持した上で自動化領域を広げるためには、工場の生産状況をリアルタイムで把握する必要があり、データ活用の質を上げていくことが必須です。そのため、部品供給〜製品組立の自動化及び生産システムへのデータ連携に取り組みました」
しかし、矢括は、稼働後の製造現場でのデータ連携の難しさも予感していた。「製造データや機器・ロボットの稼働データを収集して、これらを組み合わせた日々の生産実績データで工場を管理していくわけですが、製造現場の作業者の方々がそのデータをうまく活用できなければ、目標とする自動化は達成できません。また、全てのシステムをつないでしまうと、どこかに故障が起きた時、それが全てのシステムに波及し、工場が止まってしまうかもしれません」
そこで考えた前者の解決策の一つが、現場が見て生産がうまくいっているかどうか、見た目でわかる管理だ。「生産工程の中で、1台単位で生産する“1台流し”と“製造過程にある製品(仕掛かり)の管理を実現し、製品仕掛かりや作業手持ちが発生していれば目につくようにしました」
もう一つの後者の解決策は、どこかに故障が起きた時、それをどうリカバリーするか、どうリスクを回避するか、といった視点を採り入れて工場の設計を行うことだ。「合言葉は“止めない・止まらない工場”でした。その成果の一つは、収集したデータをAI分析し、フィードバックする仕組みを導入したこと。例えば、ロボットの稼働データを収集してAI分析することで、故障予想日を事前に計画し、保全を行うような運用も可能になります」
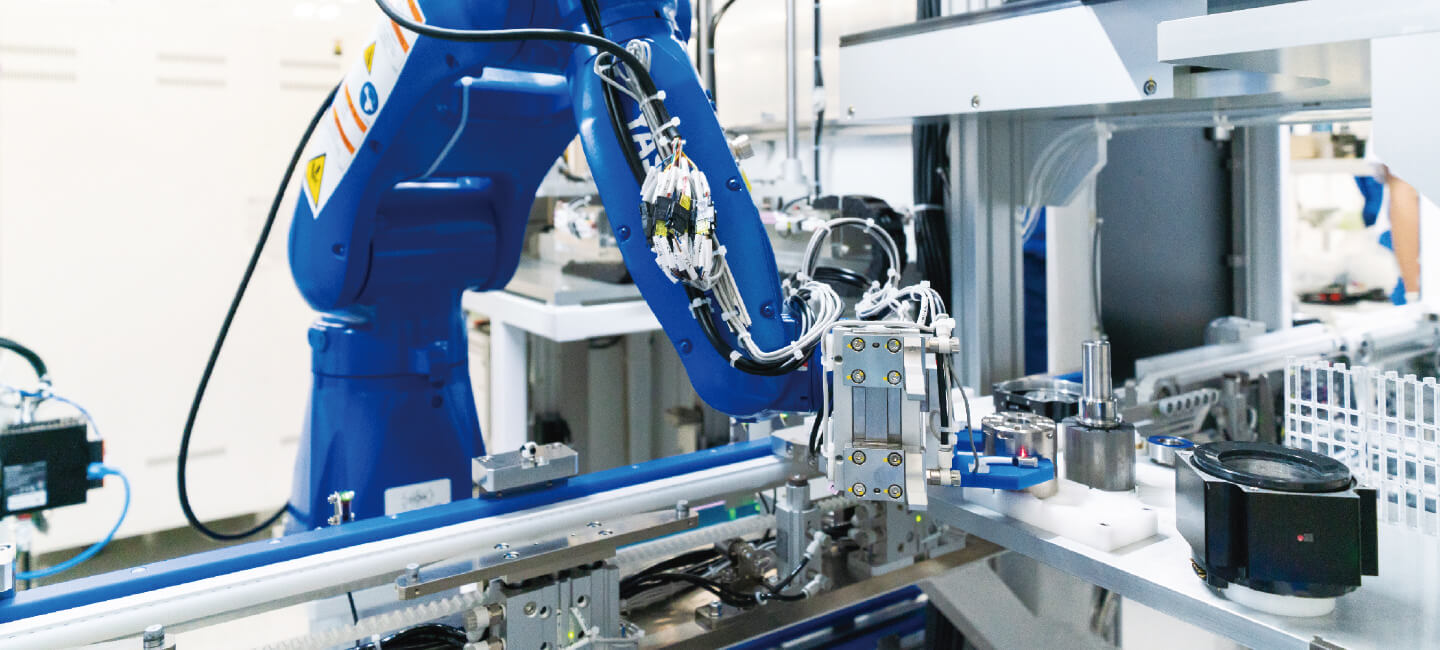
AGV(無人搬送車)の導入で
省人化を実現
工場の工程設計・生産ラインの構築の過程では、予想外の“気づき”もあった。それは、工場内の物流の自動化の必要性だ。「生産性3倍達成を徹底的に追求した時、人が倉庫から部品を運んだり、空箱を戻したりする作業も自動化しないと効率が悪いだろうという視点が初めて出てきたんです」
物流の自動化が実現できなければ、到底、目標は達成できない。そこで導入したのが、AGV(無人搬送車)だった。工場内で18台ものAGVが稼働し、20数カ所のAGVステーションの間を行き来しながら、部品を運んだり、空箱を戻したりする。これを実現するには、当然のことながら、各種工程の機器とAGVが同じ情報を共有したシステムになっていなければならない。「AGVと機器が普通に会話するようには比較的容易にできるのですが、『まだ、その部品を持ってこなくていいのに・・・』とか、『持ってくるのが遅い』など生産性向上に効果を発揮する会話まで進化させるのは至難の業です。しかし、それをクリアしないことには、AGVを導入したところで生産性向上には何の効果も出ません」
矢括は時間をかけて試行錯誤しながら工程設計に取り組み、最終的に、AGVを活用し、倉庫から生産順にタイムリーに部品供給する仕組みを構築した。
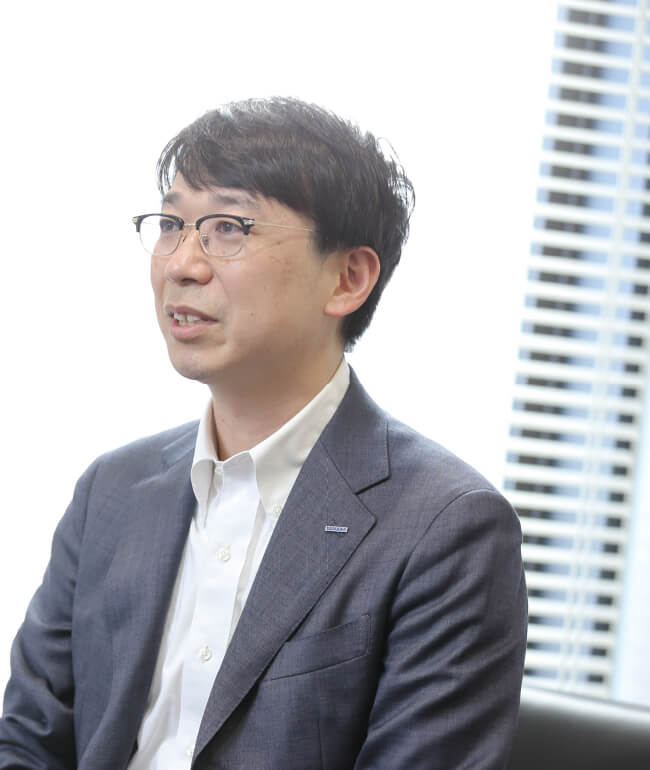
「Y’s production25のさらなる進化」
へ向けて、
さらなる挑戦は続く
矢括たちプロジェクトチームが幾多の技術的課題を乗り越えて構築した、Y’sFが生産稼働を開始したのは2018年7月。矢括が当プロジェクトに参画して約1年4カ月後のことだった。「これほど短期間のうちに、前例のない“ほぼフル自動化”した工場が構築できたのは、長年にわたって安川電機が蓄積してきた様々な自動化技術と、自動化設備へのチャレンジの歴史があったからこそです」
とはいえ、「生産性3倍、リードタイム6分の1」を達成するまでには、稼働後も長い試行錯誤が続いた。今回、当プロジェクトでは、製造現場をデータでつなぎ、生産実績、生産効率、生産時間、設備の稼働率などを「視える化」するプロダクションダッシュボードを開発。稼働後はプロダクションダッシュボードで日々操業状況をモニタリングしている。「操業状況を見ながら、目標達成を目指して、改善PDCAの取り組みをタイムリーに行っていきました」
目標が達成できたのは、2019年を迎えた頃。当初は「無理だ」と思えた高いハードルを越えた時、矢括はその喜びに浸る間もなく、すでに次の目標を見据えていた。「今回の目標は達成しているのですが、お客さま満足という点ではまだ100点ではありません。お客さまニーズのQCD(品質・コスト・納期)に対して、いかに高いレベルで応えていくか。これからも挑戦は続きます」
次なる挑戦に向かう矢括の原動力となったのは、Y’sFを見学されたお客さまからの言葉だった。「生産技術に精通したお客さまから、現場を知り、生産データを活用している点を評価していただきました。自動化するだけではうまくいかず、データで何かに気づいて分析し、最後は3現主義(現場・現物・現実)で裏付け確認し、対策実施をする。愚直にPDCAに取り組むことが次世代工場成功への鍵だと実感していましたし、そのことに共感していただけたことがうれしかったですね」
そして今、矢括は大きな夢を抱いている。それは、「Y’s production25をさらに進化させること」だ。「今は一つの工場の中だけで完結する自動化工場ですが、この先、各国の工場とデータでつなげることができれば、よりQCD(品質・コスト・納期)の視点で生産性向上を図ることができるようになると思います」
矢括と安川電機は、「Y’s production25」のさらなる進化に踏み出した。